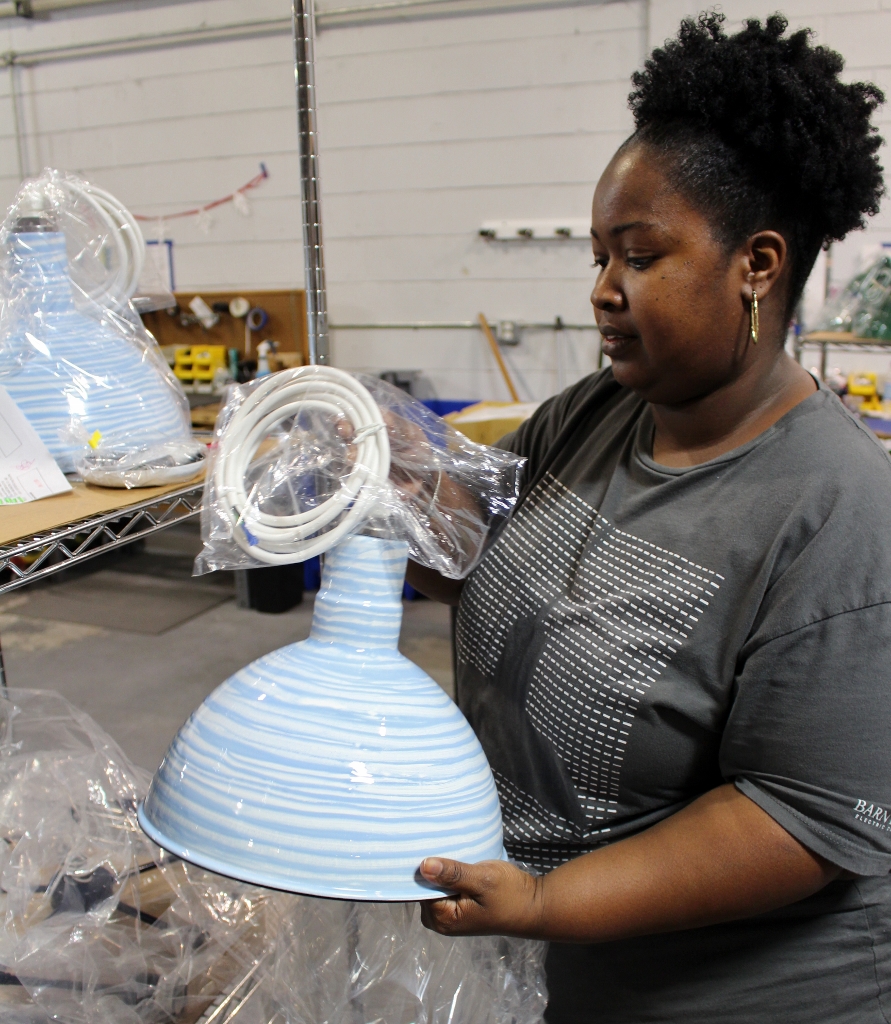
Behind the Scenes | Quality Control Team Keeps Close Eye on Thousands of Parts
With a practiced touch, Pam runs her fingers around the rim of a large, aluminum light shade. She’s feeling, and looking, for any imperfections in the piece before sending it on to inventory. Pam has worked in quality control for more than 15 years; the last five with Barn Light Electric.
“We check the raw parts as they come out of the machine shop,” Pam explains. “We’re looking for dents or imperfections, and we check that the rims are closed. We also measure to make sure the dimensions are correct and the holes are the right size.”
Pam (shown above) serves as the lead for Barn Light’s QC team which also includes Joanie and Barb (below). This trio follows every part that goes through the manufacturing process from raw metal to paint to assembly. Their goal is to verify that each piece is of the highest quality and that, when assembled, the fixture is both functional and beautiful.
“It’s a very visual inspection which is important, because if you’re buying something from Barn Light Electric, it’s usually because you like the way it looks,” Pam explains. “Customers like the looks of a piece, but quality is the most important factor to us.” She adds that their focus is to ensure that the product and the manufacturing process are not only consistent but are in line with customer expectations.
As each part moves through manufacturing, all three ladies sign off at different stages. After the finish work is complete, they check to make sure the fixture is the right color and there is no rough paint or contamination of the finish. Joanie has worked on the QC team for almost three years while Barb has logged nearly five years inspecting parts. She notes that the hardest part of the job is telling a co-worker that a part didn’t pass her inspection.
“It’s the little things that are important to QC,” Pam says. “Adding the sticker that tells the customer to use thread tape is very important for example. We check every piece of every fixture and every piece of dinnerware.” Porcelain enamel offers the toughest challenge, and Pam finds herself in the porcelain shop daily inspecting parts.
“Porcelain is the hardest because people expect so much from that finish,” she says. “We have to make sure it’s perfect so our customers receive a great product.” She adds that Mark and Richie, the QC supervisors, offer tremendous support when the team has questions.
“We work really well as a team,” Pam says. “We all know the processes and the steps to follow. When one of us is out, the other two step right in to keep parts moving, plus Mark and Richie pitch in too. Our goal is to get perfect parts assembled into one beautiful whole and shipped out on time to the customer.”