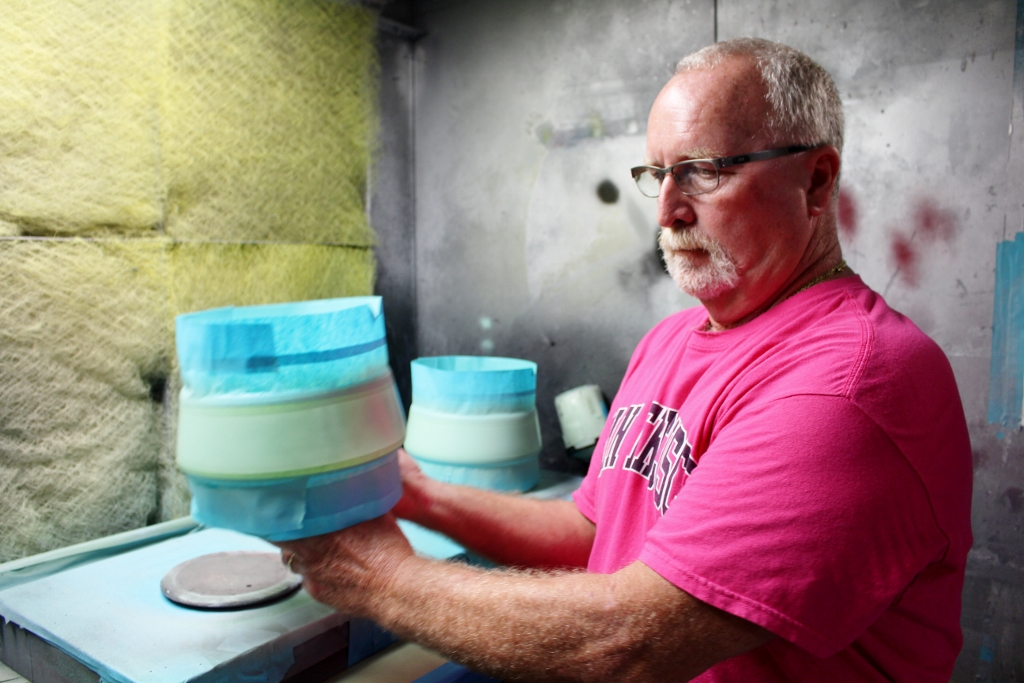
Behind the Scenes | Barn Light Electric Paint Department
Creating handcrafted lighting from scratch requires high-quality materials, a multitude of steps, and plenty of hands. Luckily, we have an abundance of all three to create our vintage-inspired barn lighting and porcelain enamel lighting here at Barn Light Electric.
After light shades are spun from raw metal in the machine shop, they are prepped for painting. Depending upon the metal used, shades are either powder coated, galvanized, or sent to the porcelain department for finishing. Shades crafted from live metals such as copper and brass require their own special finishing techniques.
Today, we visit the paint department where Nate leads our wet spray team. An Ohio native, Nate has lived in the Sunshine State for more than 30 years. He has been a vital part of the Barn Light Electric family for more than five years.
“I make sure everything is running smoothly in the department and that everyone on the team has the tools and supplies they need to do their job,” Nate says. “We have 10 team members who handle hundreds of parts each day.”
More than 200 shades receive wet spray each day while between 500 and 600 shades are galvanized. Two dozen schoolhouse globes receive attention on a typical day and dozens of copper parts make their way through the department as well.
“Every finish has different issues,” Nate explains. “The most challenging part is when we have a new product come through. It’s a learning process, but we find the best way to produce top-quality products for our customers. The one thing I always stress to the team is to imagine that light fixture going up in your own home. You want the customer to be as proud to install it as you would be.”
In his spare time, Nate loves to garden and go camping. He is married with a large extended family including two daughters, two stepdaughters, one stepson, 24 grand kids, and two great grand kids.